Have you ever wondered how companies ensure that their products or processes are reliable and safe for their customers? One of the methods that they use is called Failure Mode and Effects Analysis (FMEA). FMEA is a process that helps companies identify and evaluate potential failures in their product or process design, and determine the effects of those failures on the customer.
Jump To Section
What is FMEA?
FMEA stands for Failure Mode and Effects Analysis. It is a structured approach to identifying and evaluating potential failures in a product or process design. FMEA is used to identify and prioritize potential failure modes based on their severity, occurrence, and detection. This helps companies to focus their efforts on the most critical failure modes and take corrective action to prevent them from occurring.
How FMEA Works: Step-by-Step
Step 1: Breaking It Down
When I first learned about FMEA, I was amazed at its simplicity. We start by breaking down a product or process into smaller parts. Think of it like taking apart a toy to see how it works. Each piece matters, and we look at how each one might fail.
Step 2: Finding Weak Spots
Next, we put on our detective hats. We ask, “What could go wrong?” For example, in a car engine, a piston might crack. I’ve seen this happen, and it’s not pretty! By thinking about these “failure modes,” we’re already one step ahead of problems.
Step 3: Understanding the Impact
Now, let’s think about our customers. How would a failure affect them? If that piston cracks, the whole engine might stop working. This step helps us see the bigger picture.
Step 4: Ranking the Risks
Here’s where it gets interesting. We look at three things:
- How bad would the failure be?
- How likely is it to happen?
- How easily can we spot it before it causes trouble?
I like to think of this as a game of “Hot or Not” for problems. It helps us focus on what really matters.
Step 5: Crunching the Numbers
Finally, we do some simple math. We multiply those three rankings together to get what’s called a Risk Priority Number (RPN). Don’t worry, it’s not as scary as it sounds! This number helps us decide which problems to tackle first.
By using FMEA, you’re not just fixing things, you’re leading the way to better products and happier customers. And isn’t that what it’s all about?
How can FMEA be used?
FMEA can be used in both product and process development and manufacturing. It can be used to identify potential failures in a design or process and to evaluate the effects of those failures on the customer. FMEA can be used to initiate a process, review the design, or evaluate a new process.
FMEA can also be used to identify the scope of the analysis process. It can be used to identify the potential failures that may occur in a product or process and to determine the underlying cause of a failure.
When to Perform Failure Mode and Effects Analysis
Failure Mode and Effects Analysis (FMEA) is a powerful tool for identifying and mitigating potential failures in a product or process design. But when is the best time to perform an FMEA? In this section, we will discuss the different stages of product development and production where FMEA can be used to improve quality and reliability.
1. Conceptual Design Stage
The conceptual design stage is the earliest stage of product development. During this stage, the product is still in the planning phase and the design is not yet finalized. FMEA can be used during this stage to identify potential failure modes and evaluate the impact of those failure modes on the customer. By identifying potential failure modes early in the design process, companies can take corrective action to prevent the failure from occurring in the final product.
2. Detailed Design Stage
The detailed design stage is the stage where the product design is finalized. During this stage, FMEA can be used to evaluate the design and identify potential failure modes. FMEA can also be used to evaluate the manufacturing process and identify potential failure modes that could occur during production.
3. Prototype Stage
The prototype stage is the stage where the product is first built and tested. FMEA can be used during this stage to evaluate the product and identify potential failure modes. By identifying potential failure modes during the prototype stage, companies can take corrective action to prevent the failure from occurring in the final product.
4. Production Stage
The production stage is the stage where the product is manufactured and assembled. FMEA can be used during this stage to evaluate the manufacturing process and identify potential failure modes. By identifying potential failure modes during the production stage, companies can take corrective action to prevent the failure from occurring in the final product.
5. Post-Production Stage
The post-production stage is the stage where the product is in use by the customer. FMEA can be used during this stage to evaluate the product and identify potential failure modes. By identifying potential failure modes during the post-production stage, companies can take corrective action to prevent the failure from occurring in future products.
Types of Failure Causes in FMEA
When conducting a Failure Mode and Effects Analysis (FMEA), it is important to identify the different types of failure causes that can lead to a product or process failure. By understanding the root cause of a failure, companies can take corrective action to prevent the failure from occurring again in the future. In this article, we will discuss the different types of failure causes that can be identified during an FMEA.
1. Design Failure Causes
Design failure causes are related to the design of the product or process. This can include errors in the design, inadequate testing, or incorrect specifications. Design failure causes can lead to product or process failures that can be costly to fix and can damage a company’s reputation.
2. Manufacturing Failure Causes
Manufacturing failure causes are related to the production process. This can include errors in the manufacturing process, faulty equipment, or inadequate training of personnel. Manufacturing failure causes can lead to defective products that can be dangerous to consumers and can result in costly recalls.
3. Human Error Failure Causes
Human error failure causes are related to mistakes made by personnel during the design or manufacturing process. This can include errors in data entry, incorrect assembly, or misinterpretation of instructions. Human error failure causes can lead to product or process failures that can be costly to fix and can damage a company’s reputation.
4. Environmental Failure Causes
Environmental failure causes are related to factors outside of the product or process. This can include changes in temperature, humidity, or other environmental factors that can affect the product or process. Environmental failure causes can lead to product or process failures that can be costly to fix and can damage a company’s reputation.
5. External Failure Causes
External failure causes are related to factors outside of the company’s control. This can include changes in regulations, changes in customer demand, or changes in the market. External failure causes can lead to product or process failures that can be costly to fix and can damage a company’s reputation.
6. Maintenance Failure Causes
Maintenance failure causes are related to the maintenance of the product or process. This can include inadequate maintenance, incorrect maintenance, or inadequate training of maintenance personnel. Maintenance failure causes can lead to product or process failures that can be costly to fix and can damage a company’s reputation.
FMEA Example
Let’s take a look at an example of FMEA. Suppose we are evaluating a new process for manufacturing a car engine. The process consists of several steps, including casting, machining, and assembly.
We begin by identifying the potential failure modes for each process step. For the casting step, a potential failure mode could be a misaligned mold. The end effect of this failure mode could be a defective engine block. The severity of this failure mode could be critical because it could cause a serious accident. The occurrence of this failure mode could be low because the process is well-controlled. The detection of this failure mode could be high because it is easy to detect a misaligned mold.
The RPN for this failure mode is calculated by multiplying the severity, occurrence, and detection rankings together. In this case, the RPN is 9 (3 x 1 x 3).
We continue this process for each process step and identify the potential failure modes, end effects, severity, occurrence, and detection rankings for each.
Online FEMA Tools
Online FMEA (Failure Mode and Effects Analysis) tools are becoming increasingly popular among businesses and organizations. These tools provide a convenient and efficient way to conduct FMEAs, which are used to identify potential failures in products or processes and take corrective action to prevent them. In this article, we will discuss the benefits of using online FMEA tools and some popular options available.
Benefits of Online FMEA Tools
- Accessibility: Online FMEA tools can be accessed from anywhere with an internet connection, making it easier for teams to collaborate and work on the same project remotely.
- Efficiency: Online FMEA tools automate many of the manual processes involved in conducting an FMEA, such as data entry and analysis, which saves time and reduces errors.
- Customization: Online FMEA tools offer customizable templates and workflows that can be tailored to a specific product or process, ensuring that all relevant failure modes are considered.
- Reporting: Online FMEA tools generate detailed reports that can be easily shared with stakeholders, helping to communicate the results of the analysis and the actions taken to prevent failures.
Popular Online FMEA Tools
- APIS IQ-RM PRO: This tool offers advanced features such as risk analysis and mitigation planning, and can be integrated with other quality management systems.
- FMEA-Pro: This tool provides a comprehensive suite of FMEA tools, including customizable templates, data analysis, and reporting.
- Sologic: This tool offers a range of problem-solving and decision-making tools, including FMEA, that can be used to improve quality and reduce risks.
Conclusion
FMEA is an effective method for evaluating potential failures in a product or process design. It is a structured approach that helps companies identify and prioritize potential failure modes based on their severity, occurrence, and detection. FMEA provides a way for companies to focus their efforts on the most critical failure modes and take corrective action to prevent them from occurring. If you want to learn more about FMEA, consider reviewing the VDA FMEA Handbook or the new AIAG FMEA manual.
Did you enjoy this article on what is FMEA? Don’t forget to share and subscribe for more Growth Tactics.
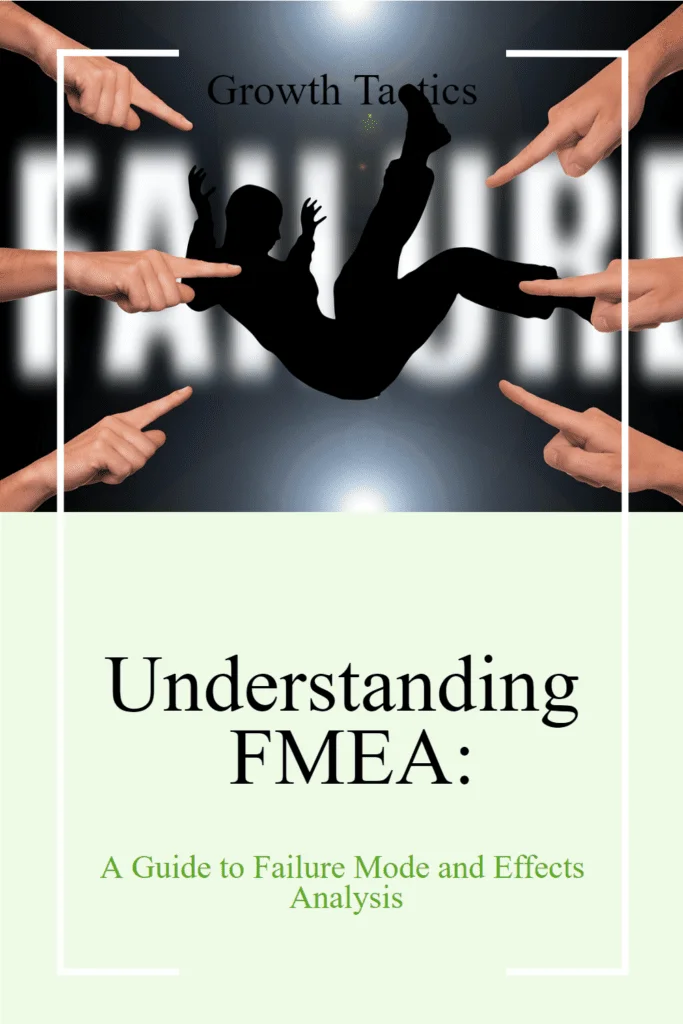