If you’re looking to improve your business processes, DMAIC in Six Sigma is an effective methodology that can help you achieve your goals. It’s a data-driven approach to process improvement that is used to improve the quality and productivity.
In this article, we’ll explore the five phases of DMAIC, the advantages and disadvantages of using the DMAIC model, when to use DMAIC, the purpose of DMAIC tools, practical DMAIC examples, and how to implement DMAIC in your organization.
Jump To Section
What is DMAIC?
DMAIC stands for Define, Measure, Analyze, Improve, and Control. It is a structured approach to problem-solving that is used to improve the performance of a process. DMAIC is a key component of the Six Sigma methodology, which is a data-driven approach to process improvement that focuses on reducing defects and variability in a process.
The Five Phases of DMAIC
The DMAIC process consists of five phases: Define, Measure, Analyze, Improve, and Control. Each phase is designed to address a crucial step in the process improvement cycle.
Define Phase
The first phase of DMAIC is the Define phase. This phase defines the problem or opportunity for improvement. It includes identifying the process to be improved, the customers affected by the process, and the goals of the improvement effort.
Measure Phase
The second phase of DMAIC is the Measure phase. In this phase, data is collected to measure the current performance of the process. This involves identifying the key metrics that will be used to measure success, collecting data, and analyzing the data to gain insights into the process.
Analyze Phase
The third phase of DMAIC is the Analyze phase. The data collected in the Measure phase is analyzed to identify the root causes of the problem. This phase involves using tools such as cause-and-effect diagrams, process maps, and statistical analysis to identify the factors that are contributing to the problem.
Improve Phase
The fourth phase of DMAIC is the Improve phase. Based on the analysis of the data, potential solutions are identified and tested. This phase involves developing and implementing a solution, and then monitoring the results to ensure that the solution is effective.
Control Phase
The final phase of DMAIC is the Control phase. The purpose of this phase is to establish controls to ensure that the improvements made are sustained over time. This involves developing a plan to monitor the process and implementing procedures to ensure that the process remains stable and continues to meet the goals of the improvement effort.
Why the DMAIC process?
DMAIC is a structured approach to process improvement that provides a framework for solving complex problems. It is a data-driven approach that focuses on identifying the root cause of a problem and implementing a solution that will improve the process. DMAIC is an effective methodology for process improvement because it provides a structured approach that can be used to improve any business process.
What are the Advantages and Disadvantages of Using DMAIC Model?
Advantages:
- Structured approach: DMAIC is a structured approach to problem-solving that provides a clear framework for understanding and improving a process. It is a step-by-step approach that helps to ensure that all aspects of the process are considered.
- Framework for solving complex problems: DMAIC is particularly useful for solving complex problems that may involve multiple factors. It provides a systematic way to identify the root cause of the problem and to develop a solution that addresses it.
- Data-driven approach: DMAIC is a data-driven approach that focuses on identifying the root cause of a problem. This means that decisions are based on data rather than assumptions or opinions.
Disadvantages:
- Time-consuming: DMAIC can be a time-consuming process, particularly if the problem being addressed is complex. It requires a significant investment of time and resources to collect and analyze data and to develop and implement a solution.
- Resource-intensive: DMAIC requires a significant investment of resources, including personnel, time, and money. This can be a barrier for some organizations that may not have the resources to dedicate to a process improvement effort.
- Not suitable for all types of processes: DMAIC may not be suitable for all types of processes. It is most effective for processes that are repeatable and measurable. Some processes may be too complex or too subjective to be effectively improved using DMAIC.
When should you use DMAIC?
DMAIC should be used when you want to improve the performance of a process. It is particularly useful when you have a complex problem that requires a structured approach to problem-solving. DMAIC is also useful when you want to identify and address the root cause of a problem.
Practical DMAIC Examples
Here are some practical examples of how DMAIC can be used to improve a process:
- A manufacturing company uses DMAIC to improve the performance of its assembly line. The company identifies the root cause of defects in the assembly line and implements a solution that reduces defects and improves productivity.
- A hospital uses DMAIC to improve the efficiency of its emergency room. The hospital identifies the root cause of delays in the emergency room and implements a solution that reduces wait times and improves patient satisfaction.
- A software company uses DMAIC to improve the quality of its software development process. The company identifies the root cause of defects in the software development process and implements a solution that reduces defects and improves the quality of the software.
Implementation of DMAIC
To implement DMAIC in your organization, you will need to follow these steps:
1. Define the problem or opportunity for improvement:
The first step in the DMAIC process is to define the problem or opportunity for improvement. This involves identifying the process that needs improvement, the customers affected by the process, and the goals of the improvement effort.
2. Assemble a project team that includes a Green Belt or Black Belt:
The next step is to assemble a project team that includes a Green Belt or Black Belt. These individuals are trained in the DMAIC methodology and can help to lead the process improvement effort.
3. Collect data to measure the current performance of the process:
The third step is to collect data to measure the current performance of the process. This involves identifying the key metrics that will be used to measure success, collecting data, and analyzing the data to gain insights into the process.
4. Analyze the data to identify the root cause of the problem:
The fourth step is to analyze the data to identify the root cause of the problem. This involves using tools such as cause-and-effect diagrams, process maps, and statistical analysis to identify the factors that are contributing to the problem.
5. Develop and implement a solution to the problem:
The fifth step is to develop and implement a solution to the problem. Based on the analysis of the data, potential solutions are identified and tested. This phase involves developing and implementing a solution and then monitoring the results to ensure that the solution is effective.
6. Monitor the results to ensure that the solution is effective:
The sixth step is to monitor the results to ensure that the solution is effective. This involves tracking the key metrics identified in step three and measuring the impact of the solution on the process.
7. Establish controls to ensure that the improvements made are sustained over time:
The final step is to establish controls to ensure that the improvements made are sustained over time. This involves developing a plan to monitor the process and implementing procedures to ensure that the process remains stable and continues to meet the goals of the improvement effort.
By following these steps, you can effectively implement the DMAIC methodology in your organization to improve your business processes and achieve your goals. It is important to note that DMAIC is an iterative process, which means that the steps may need to be repeated multiple times until the desired results are achieved.
Further Six Sigma Training and Certification
If you are interested in further Six Sigma training and certification, there are several options available to you. Here are some of the most popular options:
- Online Six Sigma courses: Many organizations offer online Six Sigma courses that cover the DMAIC methodology and provide training in statistical tools and techniques. These courses are often self-paced and can be completed from anywhere with an internet connection. Some popular providers include Udemy, Simplilearn, and Coursera.
- In-person training: In-person Six Sigma training is available through many organizations and can be a good option if you prefer a more hands-on approach. These courses are often led by experienced Six Sigma professionals and provide opportunities for group learning and collaboration. Some popular providers include ASQ, Villanova University, and GoLeanSixSigma.
- Certification programs: Six Sigma certification programs are available through several organizations, including the American Society for Quality (ASQ) and the International Association for Six Sigma Certification (IASSC). These programs typically require the completion of a training course and passing an exam. You can learn more about ASQ certification here and IASSC certification here.
- Corporate training programs: Many organizations offer Six Sigma training programs for their employees. These programs are often tailored to the specific needs of the organization and can be a good option if you are looking to develop Six Sigma skills within your company. Some popular providers include GE, Honeywell, and IBM.
Overall, there are many options available for Six Sigma training and certification, and it is important to choose a program that meets your needs and helps you achieve your goals.
Wrapping It Up
In conclusion, DMAIC is a data-driven approach to process improvement that provides a structured approach to problem-solving. It consists of five phases that are designed to address a crucial step in the process improvement cycle. DMAIC is an effective methodology for process improvement because it provides a structured approach that can be used to improve any business process.
FAQ
Q: What is the DMAIC methodology in Six Sigma?
A: The DMAIC methodology is a structured approach used in Six Sigma for process improvement. It stands for Define, Measure, Analyze, Improve, and Control, and it aims to enhance the efficiency of a process by identifying and eliminating defects and ensuring that improvements are sustainable.
Q: What are the benefits of DMAIC?
A: The benefits of DMAIC include improved process performance, enhanced quality of results, reduced costs, and increased customer satisfaction. By utilizing the DMAIC approach, organizations can systematically address the causes of problems and implement effective solutions that lead to quantifiable improvements.
Q: How do I start a DMAIC project?
A: Starting DMAIC involves selecting a good project that aligns with organizational goals and has the potential for significant improvement. It is crucial to define the project scope, identify stakeholders, and ensure that there is a clear understanding of the current process before proceeding with the DMAIC phases.
Q: What are the steps in the DMAIC process?
A: The steps in the DMAIC process include: 1) Define the problem and project goals, 2) Measure the current process performance, 3) Analyze data to identify root causes of issues, 4) Improve the process by implementing changes, and 5) Control the new process to maintain improvements and prevent regression.
Q: How does DMAIC relate to Six Sigma?
A: DMAIC is a core component of Six Sigma, which is a data-driven methodology aimed at improving quality and reducing defects in processes. Six Sigma and DMAIC work together to provide a framework for identifying problems, analyzing data, and implementing effective solutions in a structured manner.
Q: What are the phases of the DMAIC process?
A: The phases of the DMAIC process are: 1) Define – outlining the project goals and customer requirements, 2) Measure – collecting data on current performance, 3) Analyze – identifying root causes of issues, 4) Improve – developing solutions and implementing changes, and 5) Control – establishing a control plan to sustain improvements.
Q: How can I select a good project for DMAIC?
A: To select a good project for DMAIC, consider factors such as the potential impact on organizational goals, the availability of data, stakeholder involvement, and the feasibility of implementing process changes. Projects should ideally focus on areas where there are known issues or opportunities for quality improvement.
Q: What is the role of a process owner in a DMAIC project?
A: The process owner is responsible for overseeing the DMAIC project and ensuring that the process improvements are aligned with organizational objectives. They play a critical role in facilitating communication among stakeholders, providing resources, and supporting the implementation of the new process.
Q: How can statistical process control be used in DMAIC?
A: Statistical process control (SPC) can be used in the Measure and Control phases of DMAIC to monitor process performance and ensure that improvements are maintained. Control charts are often employed to visualize process variations and help identify when corrective actions are necessary.
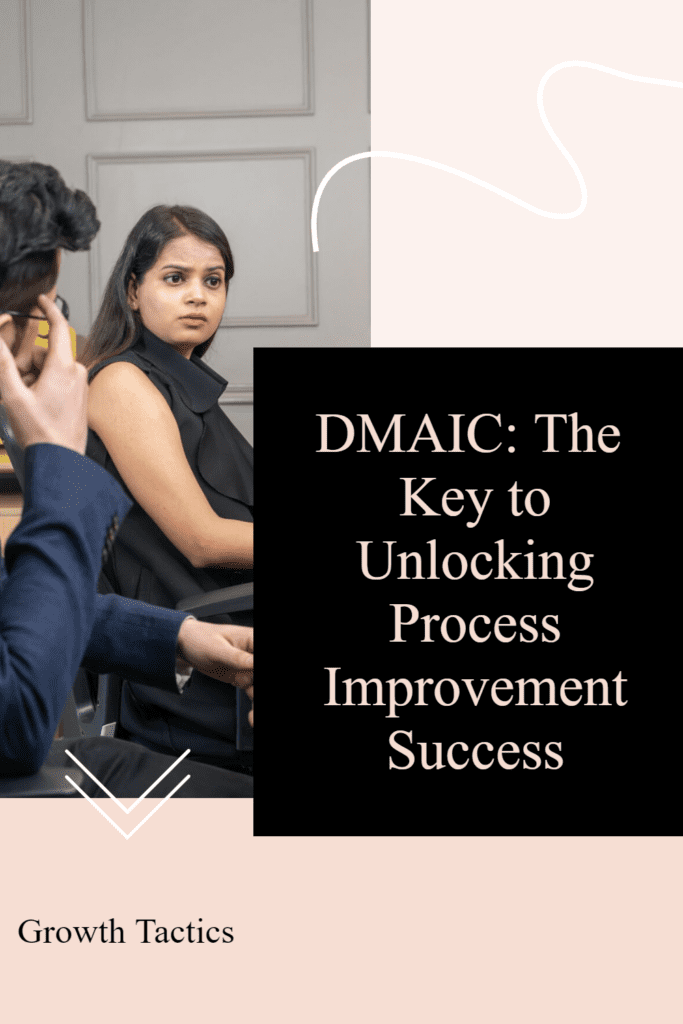